17.06.2021-08.30 – Martedì 15 Giugno si è tenuto un incontro on-line organizzato da Stain per approfondire i temi legati alla digitalizzazione della produzione, tema particolarmente sentito oggi, visto quanto si sono rilevate indispensabili le tecnologie in una situazione complessa come quella appena attraversate.
Tra le tecnologie abilitanti Industria 4.0 ci sono sicuramente i sistemi Mes per la raccolta e gestione dei dati di produzione, anche da remoto, e oggi ne abbiamo parlato con Claudio Morbi, Ceo di Stain- Mes Solutions, Roberto de Miranda, Membro del Comitato Esecutivo di Ori Martin e Antonio Lucarelli, Responsabile dei Sistemi digitali di Ori Martin.
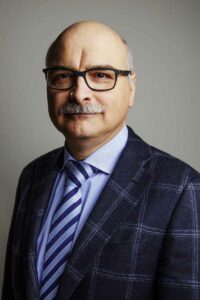
Claudio Morbi, Ceo di Stail Srl, azienda che da oltre 30 anni sviluppa software per la raccolta e gestione dei dati di produzione, cha elencato le principali funzionalità di un sistema mes, prima tra tutti avere a disposizione dati di produzione certi e in tempo reale; Morbi ci ha tenuto a sottolineare che il Mes non è un semplice software, e che per approcciare nella maniera corretta un progetto Mes serve una roadmap con obiettivi aziendali ben precisi, metodologia, organizzazione, persone, formazione, tecnologia, soprattutto in settori complessi come il metal.
Il Case Study Ori Martin
Ce lo conferma Roberto de Miranda, membro del comitato esecutivo Ori Martin, Gruppo siderurgico con sede a Brescia che da anni ha implementato il sistema Mes di Stain per la raccolta di lati di produzione e tracking del prodotto.
Ori Martin produce 700.000 tonnellate di acciai speciali all’anno per automotive e meccanica, ed è un gruppo industraile fortemente integrato a valle e a monte, in grado di eseguire lavorazioni dalla raccolta al trattamento dei rottami parco rottami fino al componente finito, oltre 1000 prodotti diversi per automotive, settore ferroviario, edilizio e meccanico. Il gruppo nel 2019 ha chiuso con un bilancio di oltre 600 mln di ricavi e EBIDTA maggiore del 10% – chiudendo in utile anche nel 2020.
Una visione, quella di Ori Martin, fortemente proiettata alla digitalizzazione, tanto che il loro progetto di trasformazione digitale è uno dei 4 progetti lighthouse Italia selezionati dal Mise, e ha come obiettivo la realizzazione di un esempio di fabbrica intelligente con reti di comunicazioni estese, affidabili e sicure, capaci di mettere in comunicazione macchinari, impianti, strutture produttive, sistemi di logistica, magazzino, canali di distribuzione, nonché fornitori e clienti. In una parola, diventare la prima Cyber acciaieria in Italia
Il percorso di trasformazione digitale di Ori Martin – lighthouse acciao 4.0
Uno dei principali aspetti del progetto è appunto la Raccolta Dati Centralizzata, con un “ capo turno elettronico”, un sistema intelligente che regola i turni in fabbrica, un sistema che impara dall’uomo, questo non per ridurre personale ma per trasferire alla macchina parte del knowlege, in modo che non vada perso con il cambio di figure professionali o il passaggio generazionale; Un atro obiettivo importante e molto caro a Ori Martin è quello di ridurre le emissioni attraverso la digitalizzazione tecnologia.
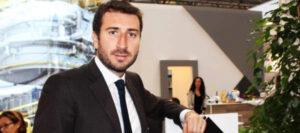
De Miranda afferma che: “Ci siamo resi conto che per implementare tutto questo è necessario avere sistemi sul campo sistemi che lavorano a perfezione, da qui l’esigenza di avere un Mes sempre più performante. L’inserimento del Mes è partito molti anni prima con Trafilati Martin, risale agli inizi del 2000 e poi abbiamo scelto di implementare Stain anche in altre aziende del gruppo.
I principali obiettivi nella scelta di un sistema Mes erano: eliminare la carta dall’ambiente di produzione, Tracking in tempo reale del prodotto, aspetto quest’ultimo fondamentale in una produzione MADE TO ORDER e non made to stock con tantissimi prodotti, e una filiera produttiva che comprende fino a 10 lavorazioni da rottame al prodotto trafilato; infine, controllo sui consumi.
Dove si inserisce il progetto Mes Stain
L’installazione del Mes è stato un percorso non privo di ostacoli “abbiamo dovuto operare un vero e proprio change management e rimodellare l’organizzazione di fabbrica”, formando e coinvolgendo anche gli operatori, che sono stati sensibilizzati e responsabilizzati dai dati.
I vantaggi ottenuti sono molti: tracking del prodotto e mescolanze in tempo reale, eliminazione della carta, risposte rapide ai clienti in caso di reclami o non conformità, maggior controllo dei costi, disponibilità a tutte le funzioni aziendali di informazioni correlate in automatico su: prodotto, processo, qualità, ordini di produzione, alimentazione con dati puliti ed affidabili dei software di intelligenza artificiale e machine learning per la manutenzione predittiva, il miglioramento continuo della qualità di processo e prodotto, e possibilità di prendere decisioni data driven e non basate su istinto. L’impatto che ha avuto l’introduzione del Mes va al di là del semplice tracking del prodotto: oggi con la condivisione del dato c’è una definizione più chiara per tutti degli obiettivi, i reparti ora si parlano tra di loro, il Mes permette di sapere cosa sta succedendo nell’altro reparto – e il personale è più motivato. E tutti questi aspetti oggi sono requisiti fondamentali che soprattutto i clienti Automotive internazionali (clienti dei ns clienti) richiedono quando vengono a fare le due diligence.
Antonio Lucarelli, Responsabile dei Sistemi Digitali, chiude confermando che il che Mes, integrandosi e comunicando con l’automazione di base dell’azienda, è un vero valore aggiunto, perché “si controlla solo ciò che si musura”. Da quando il Mes Stain è andato go-live nel gennaio 2019, il sistema ha gestito oltre 15. Ml di comunicazioni, e tracciato oltre 500.000 colli.
Il video completo del webinar: